Yamaha Guitar Development is a custom shop in Calabasas, California, where luthiers build acoustic, electric, and bass guitars for Yamaha artists. The shop is also a research & development facility, contributing to production guitars that are available to customers around the world. In this interview, Master Acoustic Guitar Designer and Luthier Andrew Enns talks about his approach to the craft and his collaboration process with the engineers in Japan.
My goal at Yamaha is to combine my intuition as a builder with the engineering know-how and technological capabilities of our Engineers in Japan to essentially break the code for total control in shaping sound of an acoustic guitar.”
Yamaha Guitar Development is a custom shop in Calabasas, California, where luthiers build acoustic, electric, and bass guitars for Yamaha artists. The shop is also a research & development facility, contributing to production guitars that are available to customers around the world.
In this interview, Master Acoustic Guitar Designer and Luthier Andrew Enns talks about his approach to the craft and his collaboration process with the engineers in Japan.
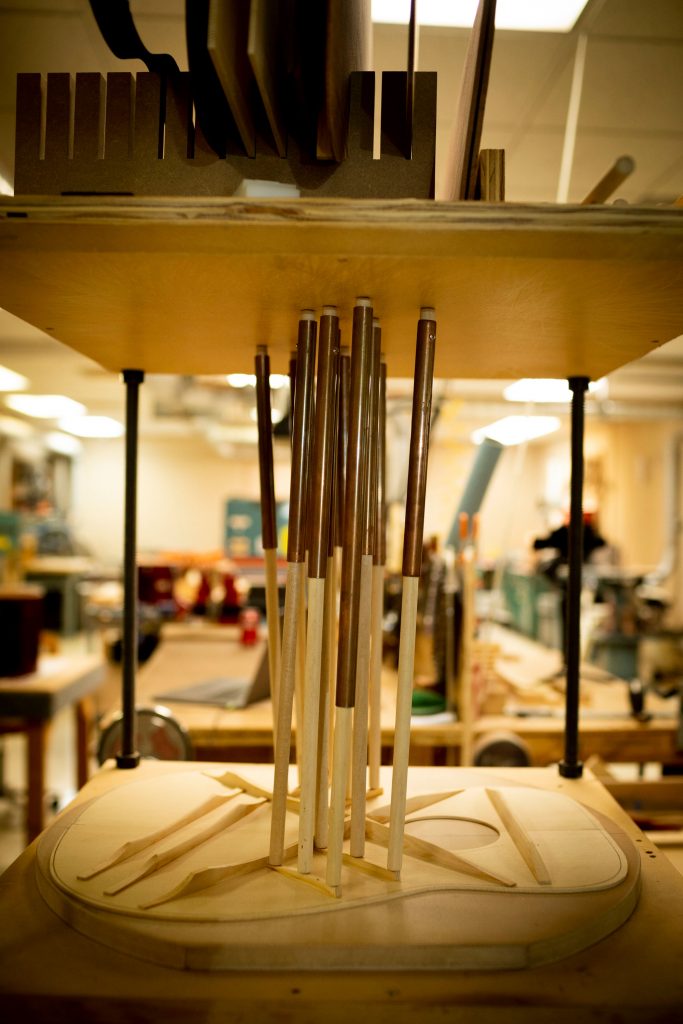
How did you get into guitar building?
Before I started building acoustic guitars, I was building electric guitars as a hobby. Then I got a job building classical guitars and learned acoustic guitar construction from world renowned master luthier Kenny Hill. From there, I learned everything I could from Kenny and other acoustic builders I met then applied that knowledge to my guitars.
Tell us about your approach to the craft
My approach is very traditional. I’m not trying to reinvent the acoustic guitar —I am trying to make a better acoustic guitar. There is still quite a bit of mystery involved with guitar and what makes one sound a certain way and a seemingly identical one sound different. My goal at Yamaha is to combine my intuition as a builder with the engineering know-how and technological capabilities of our Engineers in Japan to essentially break the code for total control in shaping the sound of an acoustic guitar. Then apply it to production models.
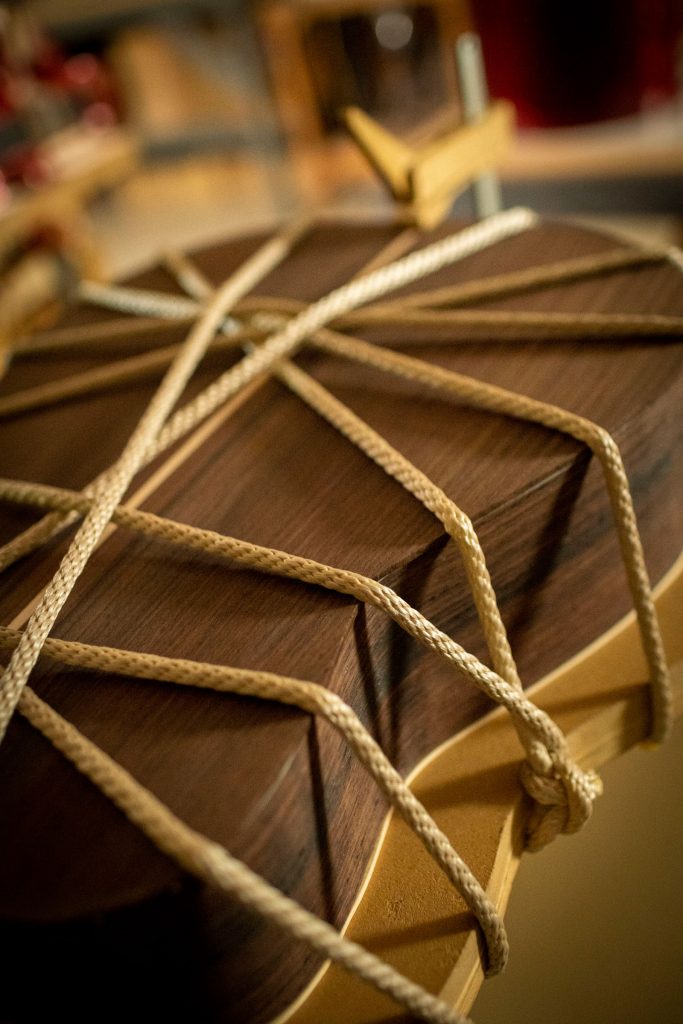
What are some of your favorite projects that you have worked on at Yamaha?
My favorite project is almost always whatever I am currently working on. Sometimes I look back and think of a specific guitar that really stood apart from the rest. But mostly, I’m always in the mindset that the guitar I am building now is going to be the best one yet.
What is the connection between R&D at the YGD custom shop and production models people buy in stores or online?
All new Yamaha models go through the development process before hitting the production factories, and part of that process is building prototypes. The YGD custom shop builds all the initial prototypes for potential new models. We collaborate with engineers in Japan and experiment with new shapes, materials, bracing ideas, construction methods, etc. to improve on existing designs and invent completely new ones as well.
What does the collaboration between the YGD custom shop and Japan look like?
I collaborate with the engineers on a day-to-day basis, but if we develop a new construction method or building technique that could prove to be beneficial to our production facilities, then we will help train the luthiers in Japan by making demonstration videos and written guides, or sometimes even by traveling to the production factories in Japan, China, Indonesia, and India, to assist in-person training.
Learn more about Andrew’s work in this Custom Shop Tour as part of our Yamaha Guitar Development Open House Online event: